What is the Impact Press?
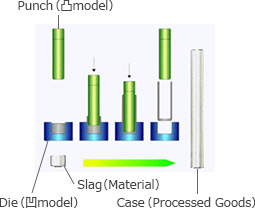
- Deep metalworking is possible at 1 type 1 process.
- Metal changes like fluid with impact pressure, and is extended along with a punch.
- Emit the heat of about 220 degrees Celsius at a moment, and change under high-pressure power.
- Residual stress is almost nothing.
- Work-hardening almost uniformly
- Only soft metal, such as aluminum and copper, is processable.
What is Deep-Drawing?
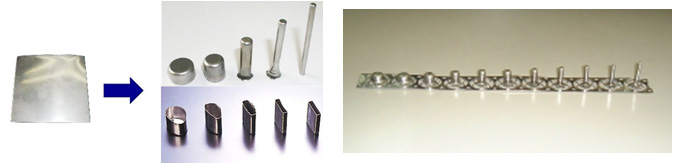
The processing method for inserting and pressing a plate material between the convex type called a punch and a dice (concave), and acquiring deep form in two or more steps.
It is the feature to seldom be accompanied by reduction in board thickness, since it extracts to the portion of the side wall deeply while material flows in from the circumference portion of the outside of a dice.
In a deep drawing processing, it divides into a process more than ten, and performs it.
When making the method object of merit, the short side will become thick from the long side.
In the stainless case that residual stress is large and metal fatigue is also large, a aging crack may occur.
*aging crack:After processing about 10 years, it makes cracks and splits.
The Advantages of the Impact Press
- The Number of Metallic Mold is less than the Deep-Drawing(Initial investment cost is cheap)
Slag punch type. An impact press die is required.
Furthermore, an ironing process is added when raising an accuracy (Ironing Processing)
In the case of deep drawing, the processing is required from 5 type to 15 type.
- The production rate is highly fit for mass-production (Low-Cost Production)
(30~100/per minute): It depends on a form and a size.
- Thickness is changeable by a part (For instance, bottom thickness 3mm, wall thickness 0.5mm)
The short side does not become thick like “deep drawing”, it is possible to make same thickness for the short side and the long side.
- There is almost no residual stress and there is intensity.(There is little crack emanating by the thermal deformation and vibration at the time of welding)
In the case of deep drawing, there is much deformation as the case upper part.
In the case of impact pressing, the metallographic structure becomes small, and intensity comes out.
- Few material losses.
In the case of an impact pressing, although a loss comes out at the time of a slag punch, since slag production is carried out by the rolling manufacturer. It melts and since it is recyclable, there are few losses.. The trimming waste after impact serves as a loss.
In the case of deep drawing, since it pierces more nearly circularly than a roll board and extracts, the loss of scraps (skeleton) is large. It becomes a loss about 30~40% by skeleton and trimming.
- Easy to make deep form.
The deep container shape more than half of a stroke of a press can be made.
Molding is possible to 170mm (including end price)of square shapes at the 300mm stroke in our company.
The deep drawing can be extracted about 1/3 of a press stroke. (the case of the press stroke , up to about 100mm)
The Disadvantages of the Impact Press
Disadvantage
- The processing quality of the material is limited.(Quality of the material which is soft as for aluminum, copper, soft steel, etc., and is extended easily)
The soft quality of the material close to pure aluminum .(A1050,A1070,3003,etc)
A5052 and A6061 are possible by form. (The small thing of growth is possible., the life of metallic mold is short.)
Neither stainless steel nor carbon steel material is processiable.(It may be possible by special processing methods, such as hot forging.)
When material hardness increases, there is a tendency for a mold life to become short. However, such as the metallic mold coating can lengthen a mold life.
- Hard to take out thickness accuracy of dimension.
For this reason, it was used only for products with a comparatively low accuracy demand, such as a marker axis for stationery, and a spray container, until now.
Moreover, when thickness is made thin, there is a tendency out of which accuracy cannot come easily. Accuracy comes out of a cylindrical type comparatively simply. The ratio of the long side of a long direction object to the short side is more difficult for a larger thing.
In the case of a cylindrical can, ±5/100 is satisfactory and accuracy come s out of an outside dimension. In the case of a prismatic can, it is less than ±1/10 only by an impact pressing.
Furthermore, it is possible to ±5/100 by adding a finishing press processing. (Research is advanced by cooperation of Nippon Institute of Technology and the Koga Laboratory. April 2012 Patent Application.)
→Sanshu Industries realized accuracy which was not made with the device of metallic mold form or lubricating oil until now.
Process of the Impact Press
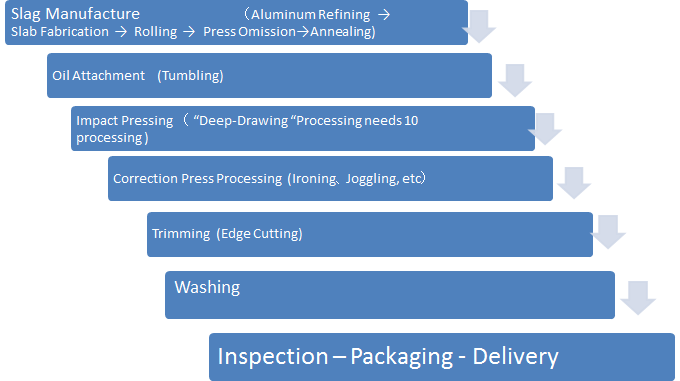
Comparison of the Impact Press and Deep-Drawing
|
Impact Press |
Deep-Drawing |
Number of Metallic Mold |
2 Model
*Initial investment cost is cheaper |
10 Model |
Thickness |
Setup is arbitrarily possible
The long side and the short side can be set as the same thickness |
A base material determines thickness.
A set-up of result thickness is difficult.
The short side becomes thick |
Process Number |
Only one part of drawing processing. |
More drawing processing due limiting proportion. |
Production Rate
(Speed) |
30 ~ 100/min
*The cost of one piece is cheaper |
10 ~ 50/min |
Processing Accuracy |
Generally it is hard to come out of surface-of-a-wall thickness accuracy.
If ironing is added, accuracy will increase further.
The present capability is that high precision for ±0.07mm by 0.8t |
Thickness accuracy is high.
(±0.05mm less) |
Process Hardening |
Become almost Uniform
Metal organization becomes fine and Hardness becomes high. |
Uneven in many cases
More drawing processing makes breakable |
Remaining Stress |
Almost Nothing.
Little Heat Modification |
May be Large by From.
Stress concentration to an opening part with the big amount of drawing processing. |
Material |
Slag (Aluminum lump) |
Board Material (Roll Material) |
Material Loss |
10% (Only Trimming Loss) |
30% ~ 40%(Skeleton, Trimming Loss) |
Processing Quality of Material |
A1050,A1070,A3003,A3005 |
Use is broadly possible |
The Merit in the Impact Press Can
- Expansion of Battery Capacity
- Improvement in Battery Safety (Raise in the intensity of a case)
With the same quality of the material, the degree of buckling intensity and pressure intensity are high in comparison with deep drawing .
- Cost reduction by high cycle production.
- Reduction of the initial cost by reduction of the number of metallic molds die.
⇒The possibility of battery development increases that it is easy to examine since a prototype cost declines.
- Reduction o f the cost by the improvement of the material yield, and reduction of an environmental impact.
The Merit of the Impact Press Products of Sanshu Industries.
- Correspondence in fine specification is possible by the its company design of a production facility, and an assembly.
Moreover, the improvement in the speed and the poor improvement of a line towards future mass production can also be made at their company.
- Since zinc is not included in press processing oil, a bad influence does not appear in the electrolytic solution in a battery. (It contributes to safety and reliability)
- The aluminum case of high intensity can be supplied by original high precision impact press technology.
- The compound coating technology which realizes a mold life equivalent to deep drawing is developed.
- Although an impact metallic mold has early wear, it becomes possible to lengthen application limits by adding a “ironing process."
Prismatic Cell Development Process
1. The Square-Shaped Impact Press which is Not made simply
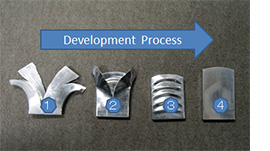
- Since history was long, our company could do the cylindrical type comparatively simply at the cylindrical can.
However, he method object can of merit with a big aspect ratio was not easy.
- It turned out that the flow of aluminum is controllable by metallic mold nose geometry, this was analyzed, and the computer simulation of form optimization and an experiment were repeated.
2, Much Failures, and Trial & Error
It does not become a form in front of the difficulty of thickness accuracy.
Although the initial metallic mold was manufactured and the trial production was begun, it will not be a long rectangle shape but will split like a trumpet.
The challenge of the engineer of our company began from here.
- #1. The substitute trial production was repeated for various form of the metallic mold.
It was the time which is inelastic straight what the first stage, or repeats trial and error to be puzzled.
- #2. The inside which changes various parameters and torn part what becomes small was found.
The element which becomes good was combined experimenting by changing every one element in which escape width, nose geometry, tool temperature, material temperature, etc. are considered, and the repetition of guess -> experiment -> consideration was repeated more than half a year.
- #3. It becomes a wrinkle after vanishing a torn part with the device of metallic mold form.
We judged that a metallic mold and a lubricous element are large, and narrows down this element thoroughly.
- #4. With the further metallic mold form and lubricant device, there is almost nothing of wrinkles.
About ten times of metallic mold form were made in one year and a fine correction was repeated.
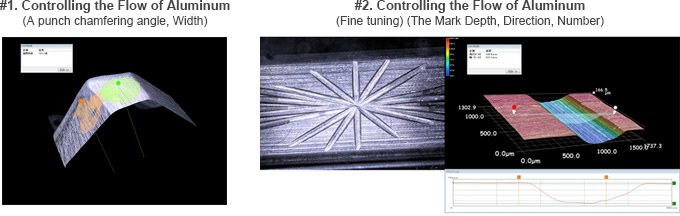
Thickness Change Explanation by Impact Press
Upper Aperture becomes Thick, and the Lower part becomes Thin
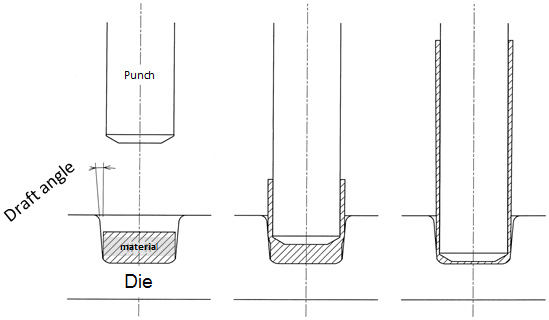
Impact Press Processing Machine & The Situation of Production
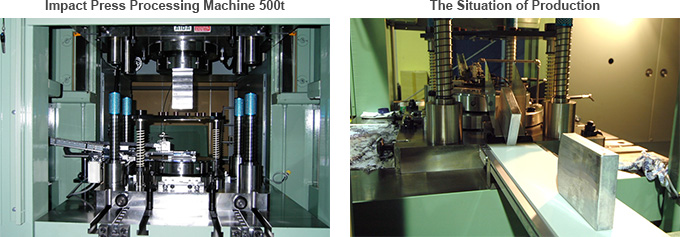
Modularization of Prismatic Can with Ribs by Impact Press
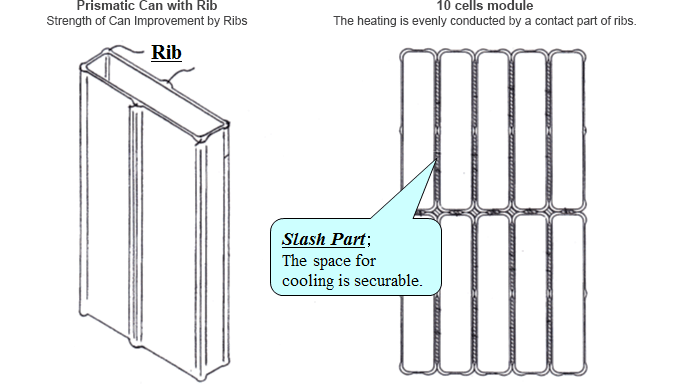